Abstract: oil decolorization is an important step in the process of oil refining. By applying the continuous countercurrent decolorization process to the refining production of soybean oil, it can effectively reduce the use of decolorizer, improve the oil yield, reduce pollutant emission, save production cost and obtain good economic benefits. Countercurrent decolorization process has two decolorization tanks and two filters - pulse filter and blade filter. The once used decolorizing agent is filtered in the pulse filter, added to the neutralized oil in the form of filter slurry for pre decolorization, and then filtered in the blade filter and discharged as waste decolorizing agent. The pre decolorization mainly removes soap and phospholipid, and the fresh decolorizing agent and the pre decolorized oil are decolorized for the second time, mainly removing pigment. Compared with the traditional decolorization process, this countercurrent decolorization process can save 30% decolorizing agent.Henan Huatai Cereals And Oils Machinery Co.,Ltd has advanced countercurrent decolorization technology, and has been contracted to build a lot of edible oil processing projects .Your complete cooking oil project solution supplier -- China Henan Huatai Cereals And Oils Machinery Co.,Ltd.
1 Introduction
Adsorption decolorization is an important step in oil refining process. In China, the decolorizing agents used are mainly clay, attapulgite and so on. In recent years, with the gradual strengthening of China's environmental protection management and the standardized management of mineral resources, more stringent requirements have been put forward for the treatment of waste decolorizer, and the procurement cost of decolorizer has gradually increased, which has brought an increase in production costs to oil refining enterprises. In view of the above reasons, domestic oil enterprises continue to optimize the decolorization process to reduce the cost of decolorization process. In this paper, the key of countercurrent decolorization process is introduced in practice, and the economic benefits of energy conservation and emission reduction of this process are briefly explained, in order to provide new ideas for oil decolorization and lay a foundation for the popularization and application of countercurrent decolorization.
2 Introduction to the principle of countercurrent decolorization
2.1 theoretical basis of countercurrent decolorization
The adsorption decolorization of oil is to use the adsorption of active and selective decolorizer to remove oil pigment and other impurities. The adsorption is mainly caused by the surface activity of the adsorbent. After the oil and the adsorbent are fully mixed at a certain time and temperature, they will finally reach the adsorption equilibrium. It has a certain functional relationship, which can be referred to the isothermal adsorption equation based on Freundlich equation [1]:
x/m=Kcn
In the formula: x---the amount of adsorbed components
M -- adsorption dose
K-- Mass transfer coefficient
C -- Residual concentration of pigment in oil at equilibrium adsorption
N - constant
When the concentration of adsorbed components in the oil gradually decreases, the adsorption effect gradually diminishes. Therefore, the adsorbent whose decolorization has reached equilibrium at one time still has a certain decolorization ability in the freshly neutralized oil. According to this principle, it is theoretically worthy of reuse, and if countercurrent decolorization is used, significant effects can be achieved.
Based on the above theory, many domestic enterprises adopt the pre- decolorization and re -decolorization continuous decolorization process [2] (referred to as pre decolorization) to reduce the consumption of decolorization process. The basic principle of this process is to contact the neutralized oil with the decolorizer filter cake layer after decolorization, and then mix it with fresh decolorizer and re decolorize after completing the secondary adsorption equilibrium. The characteristics of the decolorization process are that the decolorization process only needs to be added after the filter cake is in contact with the fresh filter for a short time. In this process, the contact time between the fresh neutralized oil and the filter cake is short. Because the filter cake layer first adsorbs soaps and phospholipids with high polarity, the outside of the filter cake layer will first be filled with decolorizing agent micropores and surfaces, which match the amount of impurities. It is easy to cause the rapid increase of filter pressure, reduce the filtration rate and reduce the continuity of production and processing. In order to ensure continuity, filter plates need to be frequently switched and changed, resulting in difficulties such as increased labor intensity. And the decolorizing agent that can be saved is relatively limited, but the residual decolorizing ability of waste decolorizing agent is still worthy of reuse, which has been proved.
In theory and practice, countercurrent decolorization, especially Ohmi process [3], will be more reasonable and scientific. Based on the above considerations and repeated demonstration, it is necessary to transform the existing single-stage decolorization process, fully consider the existing problems of pre decolorization, and add pre decolorization tank, decolorizing agent mud tank, pulse filter (or candle filter) on the basis of the existing single-stage decolorization blade filter Mud pump and decolorization pump, this process is applied to the refining process of soybean oil, which is the first in the domestic oil processing process. At present, it has been actually operated, tested and observed, and the effect is good, so as to achieve the expected purpose of saving 30% decolorizer.
3 Introduction to countercurrent decolorization production process
3.1 The basic process
Figure 1. Schematic diagram of countercurrent decolorization process
Remarks: Oil 1- The oil after passing through the pre decolorization tower; Oil 2- the oil after the secondary decolorization tower; Clay 1- clay that has been used once; Clay 2- Clay that has been used twice
The characteristics of this process are as follows:
(1) Two decolorizing tanks, one is the decolorizing tank using fresh decolorizing agent, and the other is the pre decolorizing tank using secondary decolorizing agent (mixed filter slurry of oil and decolorizing agent),
(2) Two filter systems, pulse filter and leaf filter. The pulse filter will discharge the decolorizing agent used once in the form of filter slurry and use it again. The leaf filter will dry the decolorizing agent that has been used twice. The waste decolorizing agent is discharged in the form of filter cake,
(3) The pulse filter has the function of drying the filter cake, but in this process, the filter cake does not need to be dried, but is discharged as a filter slurry with high oil content. The filter cake in the blade filter needs to be dried and then discharged in the form of dry filter cake,
(4) The filter slurry in the pulse filter can be discharged through nitrogen back blowing or grease back blowing, and the filter cake of the blade filter can be discharged through vibration,
(5) Two sets of filter oil pumps, one to transport the oil to be filtered to the pulse filter, one to transport the oil to be filtered to the blade filter, and one set of filter pump to transport the mixture of decolorizing agent and oil discharged from the pulse filter to the pre-decolorizing tank in the form of filter slurry for secondary use
(6) The pulse filter separates the filter slurry that can be transported by the pump, the oil content is 60-80%, and the leaf filter separates the waste decolorizer with about 18%-22% oil.
(7) Neutralized oil and secondary use decolorizer. The primary decolorized oil and fresh decolorizer are contacted and decolorized according to countercurrent respectively.
3.2 Process flow and description
Figure 2. Flow chart of continuous countercurrent decolorization process
The dried and neutralized soybean oil is heated to the decolorization temperature and then entered into the pre-decolorization tower with the used primary decolorizer mud and mixed with the oil. Then through the filter pump, it is transported to the vertical blade filter for filtration, and finally it is dried by steam and emptied with waste decolorizing agent. The filtered oil enters the decolorizing tank, and the fresh decolorizing agent is added to stir to make it fully mixed. After staying in the decolorization tower for a period of time, it is filtered through the filter pump into the pulse filter. After secondary filtration, the clean oil enters the buffer tank and enters the deodorization system after passing through the safety filter. During the switch, the filter slurry carried out by backwashing enters the filter slurry temporary storage tank, and then decolorization is carried out through the filter pump and the pre-decolorization tower and neutralization oil.
All the decolorization towers and buffer tanks are connected with the vacuum system, so that the system can realize negative pressure decolorization and reduce the oxidation reaction of oil in the decolorization process.
The modified process is equipped with four vertical blade filters and three pulse filters, which can realize free switching and maintain production continuity. Buffer tanks are set for once used mud and decolorized oil, which can realize the stability of on-line flow.
4 Actual process operation
After the successful commissioning of the countercurrent decolorization process, the existing 1,000t/d refinery was operated continuously for one month, and the relevant data was tracked and analyzed, and compared with before the transformation.
4.1 raw materials
Source: crude soybean oil. The main indexes are shown in the table below.
Table 1. Crude soybean oil index
The decolorizing agent is mixed with clay and attapulgite in the ratio of 2:1. The decolorizing vacuum is about 80mbar and the decolorizing temperature is 105 ℃. The decolorizing tower is stirred by steam. The amount of decolorizing agent before transformation is 15kg / T and that after transformation is 10kg / T, which is used as a benchmark for comparison. 4.2 decolorization process parameters
4.3 indicators of neutralized oil and decolorized oil
Table 2. Indexes of decolorized oil before and after countercurrent decolorization transformation
Remarks: In the above data, the amount of decolorizing agent before transformation is 15kg/t, and the amount of decolorizing agent after transformation is 10kg/t. The test data is the actual value of the factory. There is no change in the acid value before and after decolorization. For comparison of other data, see the figure below.
Figure 1. Comparison of soap content before and after countercurrent decolorization
It can be seen from Figure 1 that the soap content of decolorization, countercurrent pre decolorization and countercurrent decolorization before transformation is reduced from 50ppm to zero, and the residual soap can be completely removed after countercurrent process pre decolorization, indicating that the effect of pre decolorization on the removal of residual soap is obvious.
Figure 2. Comparison of phosphorus content before and after countercurrent decolorization transformation
It can be seen from Figure 2 that countercurrent pre decolorization has a certain effect, but its effect is not as good as that before transformation when the dosage is relatively small, but the effect is more obvious after countercurrent secondary decolorization. Even when there are few decolorizing agents, it is better than that before transformation.
Figure 3. Color comparison before and after countercurrent decolorization transformation
It can be seen from Figure 3 that the effect of pre decolorization on the removal of color in oil is not obvious, but after the secondary decolorization, even when the amount of decolorized clay is small, the color of decolorized oil is better than that before the transformation, so the transformation achieves the expected purpose.
4.4 comparison and analysis of process consumption
Table 4. Comparison of consumption before and after countercurrent decolorization transformation
4.5 cause analysis
4.5.1 establish twice adsorption equilibrium and reduce the amount of adsorbent
In the conventional primary decolorization process, all decolorizing agents are input at one time to mix the fresh decolorizing agent with neutralized oil until impurities such as pigment are adsorbed to equilibrium. Countercurrent decolorization process can establish a new adsorption balance between fresh decolorizer and the remaining pigment in the previous balance, fully improve the use efficiency of decolorizer, and reduce the dosage of decolorizer when the decolorization effect is the same.
4.5.2 Make full use of the residual polarity of decolorizer to give full play to the activity of fresh decolorizer
Decolorizer is a polar adsorbent with good selectivity and is very easy to adsorb polar impurities. Firstly, it can be neutralized in the slurry with a large amount of active soap and other polycyclic aromatic hydrocarbons, and the residual metal impurities can be adsorbed in the slurry for decolorization. First, it can be neutralized in the slurry with a large amount of active soap and other polycyclic aromatic hydrocarbons. The filtered clear oil is mixed with fresh decolorizer for adsorption to establish a new isothermal adsorption equilibrium, which can give full play to the activity of fresh decolorizer.
The countercurrent decolorization process will form a filter cake layer, recover the used decolorizing agent through backwashing, and evenly mix it with fresh neutralized oil. After mixed adsorption for a period of time and then filtration, two pressure filtration decolorization are also established, but there is a time for full mixed adsorption, so as to improve the decolorization effect. According to the actual test indicators of production, after one decolorization, the residual soap of decolorized oil is reduced to 0 and the phosphorus is reduced to below 2ppm (or lower), that is, the same amount of adsorbent adsorbs the same amount of polar impurities. When passing through the blade filter, The polar impurities on the filter cake layer are less and evenly distributed, which can avoid the decline of the filtration rate of the filter and better achieve continuous and stable large-scale production.
4.5.3 analysis of steam consumption reduction in decolorization process
In the new countercurrent decolorization process, the amount of decolorizing agent is reduced, and the service time of the blade filter is extended from 120 minutes to 180 minutes. The four blade filters reduce the number of cake blowing for 16 times. Each time, the switching and purging time is 15 minutes, with a total time of 240 minutes. The steam flow per hour is calculated as an increase of 800kg, saving 3.2T of steam in four hours, equivalent to 3.2kg/t, As the newly added pre decolorization tower increases the mixing steam by 1.2kg/t, 2kg / t steam will be saved per ton of oil.
4.5.4 Analysis of neutral oil loss reduction
The consumption of decolorizing agent is reduced, and the loss of neutral oil taken away by waste decolorizing agent is reduced, so as to save 5kg/t of decolorizing agent with 18% oil content), and the loss of neutral oil is reduced by 1kg/t.
4.5.5 Analysis of power consumption increase
Due to the addition of two pumps, one for oil transportation and one for mud transportation, the power consumption increases by 0.5kwh/t oil, but the increase of power consumption does not affect the overall economic benefit.
5.The analysis of economic benefit
Taking the soybean oil refinery with a processing capacity of 1000t / D as an example, the annual cost savings are simply calculated. It is set that the annual operation time is 300D, the soybean oil price is 5500 yuan / T, the decolorizer price is 1950 yuan / T, the steam price is 190 yuan / T, and the electricity unit price is 0.7 yuan / kWh. Combined with the data in Table 4, the calculation is as follows:
Annual cost saved by decolorizing agent: 1 950×0.005×1 000×300=2 925 000 yuan
Annual cost saved by neutral oil: 5 500×0.001×1 000×300=1 650 000 yuan
Annual cost saved by steam: 190×0.002×1 000×300=114 000 yuan
Annual increase in electricity costs: 0.7×0.5×1 000×300=105,000 yuan
The annual cost savings is 2 925 000+1 650 000+114 000-105 000=4 584 000 yuan
Because the total investment is about 5.8 million, the investment can be recovered in 1.3 years, which has great investment value.
6 Conclusion
The application of continuous countercurrent decolorization process in soybean oil refining and processing is feasible in theory and successful in practice. It can save about 30% decolorizing agent, improve oil yield, reduce pollutant emission, obtain good social and economic benefits, and has popularization significance. Henan Huatai Cereals And Oils Machinery Co.,Ltd has advanced countercurrent decolorization technology, and has been contracted to build a lot of edible oil processing projects .Your complete cooking oil project solution supplier -- China Henan Huatai Cereals And Oils Machinery Co.,Ltd.For the national storage oil with higher decolorizing agent, its economy will be more obvious. Because the process is used for the first time in China, the pre decolorization tank, decolorizing agent slurry tank and multiple pulse filters need to be added to promote the technology, and the layout and load-bearing of the existing workshop need to be comprehensively considered.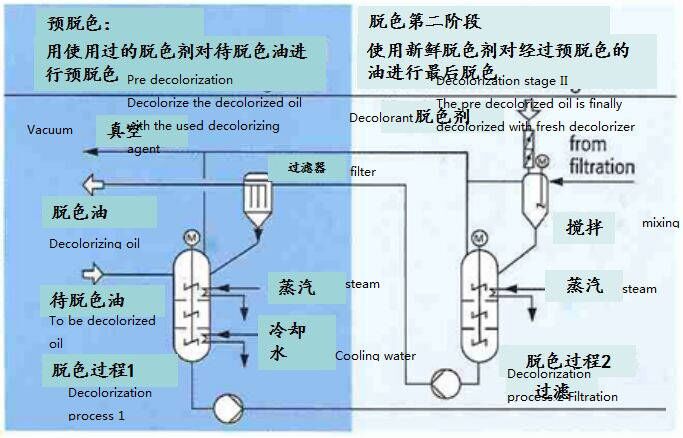